Why digitalisation is key to industry 4.0
The Internet of Things (IoT), artificial intelligence, augmented reality, big data and cloud computing have all combined.
This is delivering the era of the ‘smart factory’ - a place in which the human, mechanical and digital machine are all combining to create more efficient processes to produce higher-quality goods at reduced costs. Here, I explain why companies across all manufacturing sectors must adopt digitalisation and automation to reap the benefits for customers, employees and operations.
Real time big data
Most companies are aware of the power of big data. Integrating information from multiple digital and automated sources, analysing the data for insights and then using these insights to inform business decisions in the physical world creates a continuous loop. This has become known as the physical-digital-physical (PDP) loop.
The ultimate extrapolation of big data is the digital twin – a real-time digital image of a physical object or process that helps optimise a business performance. Advancements in processing power and digital technology now mean the digital twin which combines information and operation technology is even closer. Digital twins will ultimately allow manufacturers to have a complete digital footprint of their products and processes for their entire lifecycle, which in turn will help to inform and improve operations and drive revenue.
Smart Factories optimise process and production
The industrial IoT has the potential to save the manufacturing industry millions. Production lines become more efficient as they have less downtime thanks to enhanced machine monitoring and automated decision-making. Live product performance also increases productivity by enabling changes to be made quickly to machinery and automation in operation.
As the speed of digital transformation increases so does the competition between providers of Industry 4.0 technology. As a consequence, decreases in cost and increases in simplicity make devices like cloud analytics and sensors more readily available to all manufacturers and not just those with the money and time to implement.
Empowering employees
Knowledge is power, and many Industry 4.0 technologies are underpinned by this principle. Cloud analytics, machine to machine (M2M) technology and the Industrial IoT allow manufacturing production lines, business processes, and departments to communicate regardless of where they are in the process. The traditional silos of manufacturing are quickly removed as multiple machines in multiple locations learn from one another and the whole human workforce becomes empowered.
M2M communication needs to be embraced as it removes the human resource wasted making the same improvements across numerous locations. This gives employees the freedom to concentrate on the tasks only they can do. Industry 4.0 technologies empower people with greater knowledge of the manufacturing process which creates opportunities to innovate. This improvement of the manufacturing process also benefits the end consumer also benefits.
Compliance and regulation in industries such as the pharmaceutical and food sectors have traditionally been human resource heavy. However, track and trace, data logging, serialisation and quality inspection technologies makes complying with rules and regulations easier than ever before.
Digital transformation in manufacturing makes the human employee more agile in the workplace rather than limiting them. It can be argued that Industry 4.0 relies on the human-machine interface operating more efficiently than ever: without machine and human understanding how each other operates, the process will fail.
Evolving with Industry 4.0 is essential
The digitalisation taking place in Industry 4.0 is increasing the speed of manufacturing, making better use of resources, improving products, empowering employees, reducing costs and ultimately increasing profitability.
Less resource, material, and product waste, in particular, have never been more important as drivers to improve manufacturing. The challenges of the near future will push companies to their limits and for those which have failed to digitalise and evolve with technology they run the risk of becoming obsolete.
For more information on how Sewtec Automation can develop bespoke industrial automation systems, visit www.sewtec.co.uk.
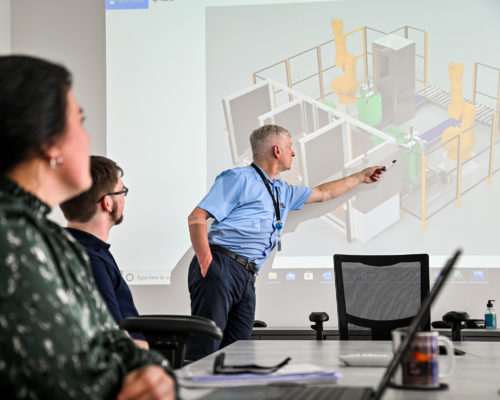