Why obsolescence is not the end for your automation system
Investing in new automation machinery when older components can no longer be supported or are obsolete is a reality faced by many manufacturers. Obsolescence can create a variety of costly issues, but is there another solution to buying a brand-new machine?
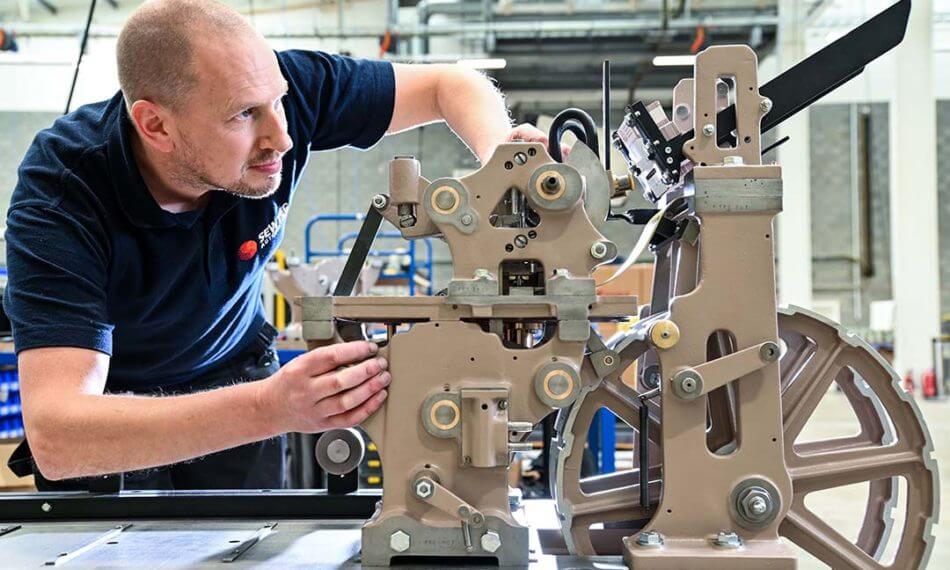
In manufacturing, obsolescence is a term used for equipment that can no longer be replaced or repaired due to an out-of-date supply chain, or because the cost to keep repairing the parts is more expensive than a new machine.
Specialist automation systems are ideally designed to perform for decades, so when equipment comes close to its end of life, manufacturers need to decide: do you continue to try and maintain the equipment or replace it altogether?
Identifying the causes of obsolescence
With the onset of Industry 4.0 and the continued, rapid development of technology, obsolescence is a challenge for many manufacturers. Issues can range from an outdated control platform, availability of critical spares, or lack of support from an existing supplier. Changing requirements for a machine may also render it obsolete, for instance if the manufacturer requires a higher output rate.
COVID-19 has heightened the risks for those manufacturers who use foreign integrators too; as travel restrictions continue to increase the threat of obsolescence if integrators are unable to assess and update machines.
The consequences of machine obsolescence
What happens when components of a machine become obsolete? It varies across manufacturers but having components of a machine no longer fit for purpose could result in a reduction of the quality of product being manufactured. This could result in more ‘rejects’ on the production line as well as the possibility of faulty products entering the market, which could damage loyalty and reputation.
The ultimate consequence of component failure is downtime of the production line. This can be costly to resolve, especially if the parts required are no longer supported and alternatives need to be sourced. A Oneserve study in 2019 for the UK manufacturing industry found that unwanted downtime costs a company on average £60,210 a year.
Finally, the safety of personnel is the most serious consideration for any manufacturer. Often older equipment is non-compliant with the latest safety standards due to changing standards or replacement parts being used which do not perform to the same level as the obsolete part, all of which can lead to accidents and potential injuries.
How to avoid obsolescence in automation
It is vital, therefore, to have an obsolescence plan in place. Knowing when parts of your equipment are likely to need upgrading or replacing is a key step in preventing unwanted downtime due to damaged machinery.
Ensure your automation provider can offer a critical spares list and agree how long these spares and components will be available. This can help with forward planning and budgeting.
The last resort for obsolete machinery
If replacing the obsolete component is no longer cost effective, most manufacturers are faced with the reality of having to replace the whole system with a brand-new automated solution.
This may be the best option but replacing old machinery comes at a price. Not only will a new automated solution be a significant investment, but it will also require full operator training, which increases the amount of time the production line is down.
The Sewtec solution to obsolete machinery
Even if it appears that a system or machine is obsolete, Sewtec can offer an alternative solution.
With an inhouse technical team and unrivalled engineering excellence, we pride ourselves on renovating and upgrading machines to run better than new, a challenge that others cannot or will not tackle.
Sewtec can de-commission and refurbish machinery, supply and reconfigure a new control system, update software, and recommission with new CE marking.
We also have a track record of enhancing existing machines by carrying out mechanical improvements, increasing throughput and efficiency, and thereby saving the need for significant investment on new automation machinery.
If you have an automated system that has become obsolete and would like a free consultation on how we can help, contact a member of the team today.
Read more about our capabilities with obsolete machinery.